The first step of plastics rotomolding is to create a mold. Once the mold is created, the plastic is injected into it and rotated until the desired rigidity is reached. When the part is completed, the plastic is removed from the mold and is ready for final inspection. The process differs from spin-casting and centrifugal casting in that it uses low rotational speeds ranging from four to 20 revolutions per minute.
Once melted, Plastics Rotomolding powder is introduced into the mold. The interior walls of the mold are coated with the plastic. The plastic then transfers to a cooling station. The product is rotated in a cooling station, exposing it to cold water and air. After cooling, the product is manually removed from the mold. Depending on the requirements, some products may need further finishing, welding, or cutting before shipping. However, most products are ready to go right from the mold.
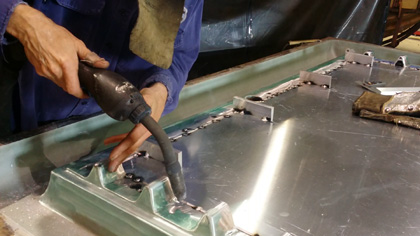
To produce rotomolded parts, the mold must be accurate. A small amount of plastic powder is applied to the mold's walls. The plastic powder is then melted and then transferred to a cooling station. The plastic is then exposed to cold water and air for 20 minutes, and then it is manually removed from the mold. Some products may require further finishing, welding, or cutting before they are ready for shipping.
Various types of rotomolded plastics are produced. Each process produces a hard, seamless, and durable piece. The finished product is usually a standalone product, or a component in a more complex product. Because of this, it requires a precise mold. Advanced Plastics Rotomolding can produce a mold with the required precision. Throughout the entire production process, the company can become your one-stop partner.
Polyethylene is the most commonly used thermoplastic for rotomolded products. Its high tensile strength and low cost make it a desirable material for a variety of applications. This material is also lightweight and can be easily transported. It is also resistant to extreme temperatures, so it is ideal for use in outdoor recreational products. This material can be shaped into many different shapes and sizes, and it is ideal for a number of different industries.
Injection molding is a popular method for producing high-quality parts with uniform wall thickness. The process is also ideal for parts that require a streamlined manufacturing process. It is especially helpful when the part is a complex component in a more complex product. The plastics rotomolding method creates a precision mold and is the perfect solution for a variety of products. With their in-house mold shop, Advanced Plastics Rotomolding is the best partner for the complete process.
The process is widely used in the manufacturing of plastics. Its advantages over metals include durability and cost, and is less expensive to ship. It also allows for more design flexibility. In rotomolding, a logo can be molded onto a product instead of being attached to it with a sticker. It also allows for a customized logo on the item. For example, a sticker might peel off over time.